The crux of the matter: facing the facts about launches & liabilities
- Renae Kiely
- Jun 27, 2019
- 2 min read
Updated: Dec 7, 2019
This week is an exciting week for the MSP team, and to say it’s been a long journey is an understatement. However, we are a down-to-earth (pardon the pun) bunch, and we realise that any space venture comes with its own set of risks and unpredictability.
Chime in the famous quote from John Swigert, who was an astronaut aboard the Apollo 13 mission:
And while, ACRUX-1’s mission doesn’t involve sending anyone to the moon and back,we are keenly aware of the risks involved with what we’re doing — especially since, when it comes to a CubeSat’s mission, success rates are on average 45% for academia and 77% for industry.
So what are some of the reasons why CubeSat missions have such low success rates? In 2017, the U.S. Space Program Mission Assurance Improvement Workshop identified that the most common CubeSat failures had to do with the communication system (radio, antenna, and ground segment); the power system (solar cells, batteries and power management boards); deployables such as antennas; and quality issues related to purchasing off-the-shelf satellite components, which generally don’t maintain documentation or “user manuals” that might help mitigate risk.
And it’s important to note that limited time, experience and access to things like comprehensive testing, funding and personnel resources had significant impacts on CubeSat mission success rates as well.
***
For ACRUX-1, we’re keeping our eye on a couple things in particular:
ACRUX-1’s first few orbits. This is when we will know whether the CubeSat’s energy harvesting and power system correctly work. ACRUX-1 is programmed to extract diagnostic information about the solar charging system, battery temperature, transmitter temperature and general health of the satellite. This information is transmitted to us through our telecommunication system so when we get our first “ping” (we call it the beacon) we’ll know how well these systems actually work.
Our orientation control system. This is the system that spins the satellite to point in different directions, and uses magnetorquers to “push” of the Earth’s magnetic field to orient itself. Our algorithms and hardware have been tested in the lab and in simulations, but we won’t know if it actually works until we put the satellite in space. This orientation system is the most complex engineering work in the satellite so there’s a lot of things that could go wrong. Once we hear the first ping, we can start testing this system by enabling it from our ground station connection.
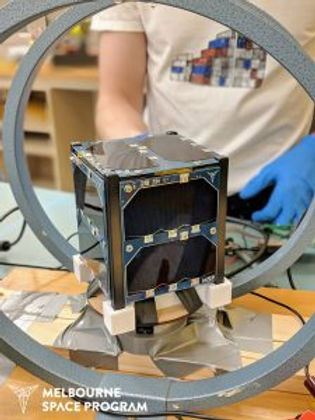
Because we’ve put our heart and soul into a complex and demanding project that we believe is unlike any other accomplished in Australia before — in spite of all the risks involved in launches and liabilities.
(And we’ve done it all as volunteers, in our spare time.)
Comments